HOUR ELECTRIC COMPANY, INC.

EST. 1979 -
Fort Edward, NY
(518) 747-4144
MAINTENANCE
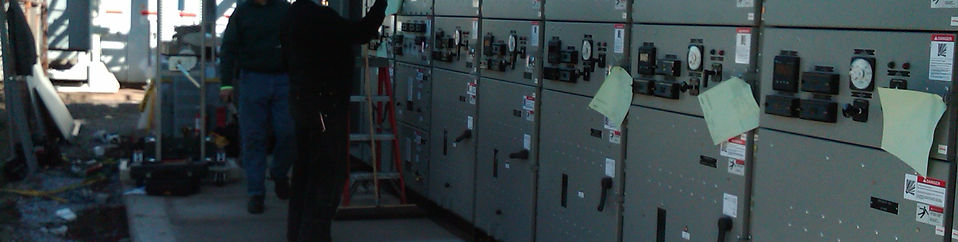
Electrical maintenance is as, if not MORE important than the original installation. Often a few hundred dollar maintenance service saves thousands over a repair, or worse, total replacement. Please have a look at some of our most popular and recommended maintenance services below:
GENERATORS
Inspection: (Recommended Interval – Every 6 Months)
74 point inspection covering critical items such as your Engine, Generator, and Transfer Switches. The Full Service also includes oil and oil filter replacement, fuel filter replacement and coolant filter replacement if applicable. Air filters will be checked but will only be changed if needed (only with approval from the customer).
Inspection Full Service: (Recommended Interval – Every 12 Months)
(If unit is used for Prime Power, recommend changing oil every 6 months or 250 hours, whichever comes first)
74 point inspection covering critical items such as your Engine, Generator and Transfer Switches. This Full Service also includes oil and oil filter replacement, fuel filter replacement and coolant filter replacement (if applicable). Air filters will be checked, but will only be changed if needed (only with approval from the customer.
Load Bank Testing: (Recommended Interval – Every 12 Months)
(Annual test is REQUIRED for Hospitals and other life support providers if a load of 30% of the generator set’s nameplate rating cannot be achieved during the required monthly test.)
Optional 2 or 4 hour testing. Minimizes potential of issues related to moisture build-up, settling of particles in fuel and carbon deposits in engine. This is not only a recommended test, but per JCAHO and Public Health regulations, is a requirement for facilities providing life support systems, i.e. hospitals and nursing homes.
Coolant System Flush: (Recommended Interval – Every 24 Months)
Reduces sediment buildup which could cause corrosion in coolant piping and tanks.
Belts and Hoses Replacement: (Recommended Interval – Every 24 Months)
Replacement of belts and hoses reduces risk of failure which could cause further damage to engine.
Battery Replacement: (Recommended Interval – Every 24 – 36 Months)
Batteries are load tested with Carbon Pile testing. Remove and replace batteries if between two and three years old at time of Inspection or Full Service Inspection. Includes disposal of old batteries.
SWITCH GEAR
It is generally recommended that metal-clad switchgear be inspected six months to a year after installation and then every five years subsequently to ensure proper performance of the switchgear. The frequency of inspections are determined by the level of the facility’s experience as well as plant conditions. Hour Electric can inspect, test and repair your switchgear per OEM specifications.
TRANSFORMERS
The cornerstones of Hour Electric's preventive program are oil sampling, electrical testing and visual inspection. Together, these three methods provide the information to analyze the condition of your transformer and switchgear and to determine the steps needed to assure reliability and top performance.
Electrical Testing
Recommended Intervals:
Liquid filled Transformers:
-
1. Liquid-filled transformers should be tested and inspected every one (1) to three (3) years, depending on the environment of the transformers and its load.
-
2. They should be tested any time that there has been a severe fault on the secondary side of the transformer, or any time that a problem is suspected in the transformer.
Dry Type Transformers:
-
1. Dry type transformers should be cleaned every six (6) months to one (1) year, depending on the environment of the transformer location.
2. They should be electrically tested every one (1) to three (3) years, depending on the environment and the load, or any time there has been a severe fault on the secondary side, or if a problem is suspected in the transformer.
Electrical tests accurately measure these important values:
-
Insulating value of insulation (DC Megger)
-
Resistive and Capacitive loss (DC Hipot)
-
Power Factor (tests of transformers & bushings)
-
Relationship of primary and secondary voltages (TTR)
-
Trip levels and accuracy of relays and low, medium and high voltage circuit breakers
Test results are compared to manufacturers specifications and/or performance standards set by NETA, IEEE and NEMA, and establish a baseline for comparison with future tests. Repairs or calibration needed to bring equipment into specification can be easily identified, and post repair testing assures that proper corrective action has been taken.
In many cases, testing identifies the need for simple repairs and adjustments that preclude costly repairs and downtime in the future.
Tests Performed
The suite of tests include the following:
-
Dielectric Absorption
-
Insulation resistance test, winding-to-winding and winding-to-ground.
-
Turn to Turn Ratio Test: to determine actual vs. calculated voltage
-
Power Factor Test: to assess condition of electrical insulation in high voltage apparatus
-
Breaker and relay tests of contact resistance, conductivity, insulation resistance, current and /or voltage trip levels
Equipment Used
-
Microprocessor based circuit breaker test sets for high current injection
-
5KV Insulation Resistance testers
-
Automated Insulation Power Factor Test Set
-
Protective Relay Test Set
-
Digital Low Resistance Ohmmeters
-
10KV automated power factor test set
-
Turn to Turn Ratio Test Set
Repairs
Our breaker and relay test process compares the performance of your equipment to manufacturer’s maintenance specifications. In addition to testing, our electrician's perform on-the-spot repairs such as:
-
Cleaning cubicles
-
Burnishing and adjusting contacts
-
Lubricating moving parts
-
Retrofitting trip units
-
Repairing faulty subassemblies
More extensive repairs are performed by returning the faulty item to the supplier and installing a new item or on a subsequent site visit.
Test Report and Analysis
After the test program is completed, a test report is compiled and submitted to our customer. The test report presents the actual data taken at the customer’s site and the results of any calculated values. Out of specification conditions are highlighted and maintenance recommendations are presented